
Home > Support > Technical info > Types of Valves
Full Guide to All Types of Valves: Functions and Applications
Ever confused about how many types of valves exist? Learn the types of valves in piping and other systems, their classifications, and how they optimize fluid control effectively. Let’s go!
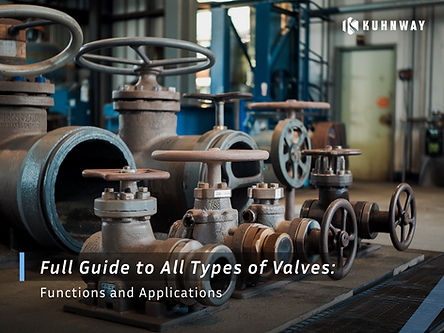
What is a Valve? What is Its Function?
A valve is a mechanical device used to regulate, direct, or stop the flow of fluids—whether liquids, gases, or slurries—within a piping system. It works by opening, closing, or partially blocking pathways, allowing precise management of fluid movement.
The functions of valves are crucial for maintaining control in any system. They start or stop the flow of fluid as needed, regulate pressure to ensure balance and consistent operation, direct fluid to specific pathways within a system, and prevent backflow that could damage equipment or disrupt processes. Moreover, valves can throttle flow rates to meet specific operational requirements and enhance safety by relieving excess pressure or vacuum within the system. Valves also help isolate sections of a system for maintenance and fine-tune flow rates in sensitive applications. From basic water supply to intricate industrial setups, valves play a vital role in ensuring safety, efficiency, and functionality.
There’s a wide variety of valves available, each with unique classifications. Let’s explore these types of valves and their applications with different classifications to uncover more of their essential roles.
Different Types of Valves

First, let’s look at the classification based on mechanical motion. There are 2 types: linear motion and rotary motion.
Linear motion valves operate by moving a closure element, such as a gate or diaphragm, in a straight line to regulate fluid flow. This design allows for precise control, making them ideal for applications requiring accurate flow modulation and tight shut-off.
Rotary motion valves utilize a rotating component, like a ball or disc, to manage fluid flow. They are characterized by quick operation, often needing just a 90-degree turn to open or close, which enhances efficiency in systems requiring rapid response.
Here are the common types of linear or rotary motion valves:
-
Gate Valve
Gate valves are one of the most commonly used valves, designed as linear motion devices with a flat or wedge-shaped gate to control fluid flow. Think of a sliding door that moves up to allow flow or down to block it, or a floodgate at the top of a reservoir. When fully open, they offer minimal resistance, providing smooth flow with little pressure loss.
These valves are best suited for on/off applications, as throttling for extended periods can damage the gate and seals. Partially opening the valve can also lead to vibrations or even damage over time.
Gate valves are widely used in water supply systems, oil pipelines, and industrial plants that require full-on/off control. Their excellent shut-off capability also makes them suitable for handling fuel, gas, slurries, steam, and other fluids. They are relatively easy to disassemble for maintenance, adding to their practicality.
However, their slower operation and larger size might make them less ideal for space-constrained setups. Despite these limitations, their reliability and durability make them a staple in many industries.
-
Globe Valve
Globe valves are designed to regulate flow using a disk that moves up and down inside a spherical body. It’s similar to turning a faucet to adjust water pressure. The S-shaped flow path allows for precise control, making them ideal for systems like steam lines, cooling systems, and fuel processes.
However, their complex design can cause higher pressure drops compared to simpler valves like gate valves. While they are more expensive, they offer better shut-off performance and more accurate throttling control. That said, globe valves aren’t suitable for fluids with particles, as they can clog easily.
These valves are also bulkier and heavier than many other types, which can be a downside in tight spaces. Even so, their precision, reliable sealing, and ability to handle frequent adjustments make them a trusted choice in industries where accuracy and dependability are critical.
-
Needle Valve
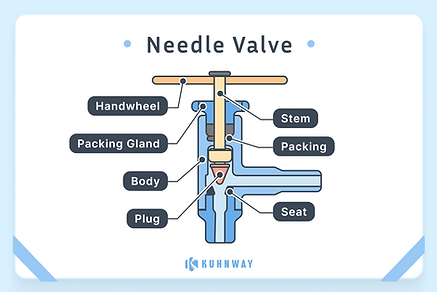
Needle valves are linear motion valves specifically designed for precise flow control. They work much like globe valves, using a long, conical plunger that fits into a small opening. Imagine a sharp needle being turned to gradually adjust the flow. This mechanism allows for incredibly fine control, making them ideal for tasks that require accuracy, like regulating fuel delivery in engines or fine-tuning experiments in a lab.
Because of their small openings, needle valves aren’t suitable for high-flow systems, but they excel in applications where precision is critical. Their durable design makes them highly reliable, especially in systems like instrumentation and chemical dosing, where even the smallest flow adjustments can have a big impact.
-
Pinch Valve
Pinch valves are linear motion devices that control flow by squeezing a flexible tube with a pinching device. Think of how you pinch a garden hose to stop water. The fluid only contacts the tube, reducing wear on the valve and preventing contamination.
With fewer components, these valves are more cost-effective and offer better leak resistance compared to other types of valves. They excel in handling abrasive slurries, viscous liquids, and fluids with suspended solids. This makes them a go-to choice in industries like mining, wastewater treatment, and food processing.
However, the tube material must match the fluid's properties and may require regular replacement. They are also uncommon for gases and other high-temperature or high-pressure uses as the tubing might deform. Despite this, their simple design, low maintenance, and effective isolation make them highly reliable.
-
Diaphragm Valve
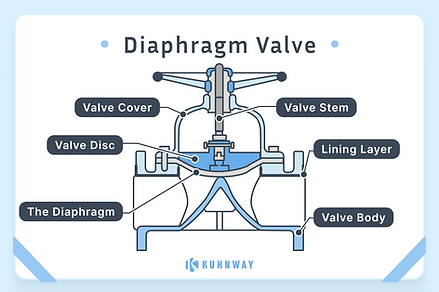
Diaphragm valves, or membrane valves, operate by pressing a flexible diaphragm against a seat to block fluid flow. Picture a drum skin being pushed down to seal an opening. These linear motion valves are exceptional at handling corrosive, sludgy, or particulate-heavy fluids, as the fluid never contacts the moving parts.
They are widely used in water treatment, pharmaceuticals, and food industries due to their clean and efficient design. However, they aren’t ideal for high-pressure systems, as the diaphragm material can wear under stress. Their ability to provide reliable sealing and easy cleaning makes them indispensable in hygienic and sensitive processes.
-
Ball Valve
Ball valves are rotary motion devices featuring a spherical ball with a hole (or a bore) through the center. A simple 90-degree turn aligns the hole with the flow path to open the valve or blocks it to stop flow. Often found in hydraulic and gas systems, ball valves are prized for their fast operation, tight sealing, compact design, and ability to handle high pressures.
There are two types: reduced-bore and full-bore. The only difference is the size of the bore as in full-bore valves, the opening matches the pipe diameter. Full-bore valves are widely preferred because they minimize pressure drops, allowing for smoother flow even in high-volume applications.
However, they are not well-suited for continuous throttling because partial openings can lead to seat erosion. Also, their design makes cleaning more challenging, increasing the risk of contamination.
-
Butterfly Valve
Butterfly valves are rotary motion devices with a disc mounted on a rotating shaft. When turned with different angles, the disc either allows or restricts flow, offering quick and efficient operation. Lightweight, compact, and cost-effective, these valves are commonly used in large-diameter pipelines, HVAC systems, compressed air or gas systems, fire protection, and water distribution networks. Their valve bodies also come in various configurations.
While butterfly valves provide rapid shut-off, cleaning them can be a challenge. Also, they can only throttle effectively when the pressure difference is low. Despite these limitations, their low-pressure drop and ease of operation make them a popular choice for controlling fluid flow in diverse industries.
-
Plug Valve

Plug valves are rotary motion devices that use a cylindrical or conical plug with a bore to control flow. Picture a cork in a wine bottle that you twist to align its opening with the spout. These valves are known for their simplicity, durability, and ability to handle a variety of fluids, including gases and slurries, since the plug's movement helps clear away particles, stopping them from building up and causing blockages.
Plug valves are commonly used in chemical processing, natural gas pipelines, oil refineries, mineral handling, sewage systems, and water treatment facilities. While they provide fast, reliable on/off control, larger sizes can require significant force to operate, and regular maintenance is essential to keep them functioning smoothly in demanding environments.
Next, let’s explore classification based on the operation mode. Here we have listed self-actuated and actuated valves.
Imagine valves that can take care of themselves! Self-actuated valves, or automatic valves work automatically, responding to the fluid’s properties like pressure or flow. No external power is needed, which makes them both cost-effective and low-maintenance.
Now, think about valves that respond to commands with precision and speed. Actuated valves rely on external mechanisms, like electric, pneumatic, or hydraulic actuators, to get the job done. They’re perfect for automated systems that need reliability and control.
Let’s look at some examples of automatic and actuated valves:
-
Check/non-return Valve
Check valves, also known as non-return valves, are automatic valves that permit fluid flow in one direction and prevent backflow. They operate with movable elements, such as a lift, tilting disk, or swing arm, which open when fluid flows forward and close automatically when the flow reverses. This simplicity ensures system protection without manual intervention by stems or handles.
However, they may not seal perfectly under low pressure or with debris. The risk of water hammer or pressure surges that could harm pipelines is another concern. Check valves are commonly used in pump discharge lines, water systems, fuel and oxidizer mixing systems, and gas pipelines to safeguard equipment and maintain process integrity.
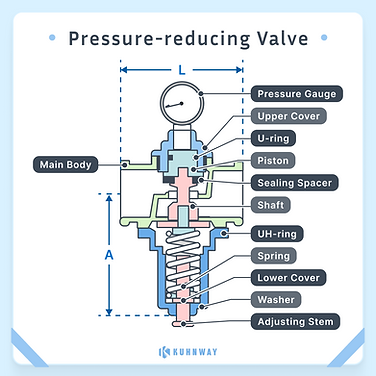
Pressure-reducing valves are automatic valves designed to lower high inlet pressures to a stable, lower outlet pressure. They maintain consistent downstream pressure, even with upstream fluctuations. These valves are essential in protecting equipment, improving safety, and boosting energy efficiency by preventing overpressure, reducing wear on systems, and minimizing noise and turbulence.
Still, they can cause pressure drops and require maintenance to avoid clogging issues. Pressure-reducing valves can be found in water distribution networks, industrial setups, and irrigation systems to ensure safe and reliable pressure regulation.

Pressure-relief valves are automatic valves that safeguard systems by releasing excess pressure when it exceeds a preset limit. They activate without external power, venting fluid until safe operating conditions are restored.
However, they have limited capacity for fine control and require regular inspection and maintenance to maintain functionality and ensure long-term reliability. Found in boilers, pressure vessels, and piping systems, these valves are vital for preventing overpressure scenarios that could lead to catastrophic failures.
Pressure-sustaining valves are automatic valves that maintain a minimum upstream pressure without dropping by opening only when the desired pressure is reached. When upstream pressure increases, the valve opens to allow downstream flow; if it drops below the setpoint, the valve closes. They are also useful for balancing pressures in ring circuits.
However, incorrect settings may lead to downstream pressure issues. These valves are widely used in water distribution systems and industrial processes to ensure adequate pressure for essential operations.
Motor valves are actuated valves operated by electric motors, providing precise control over fluid flow. They can be controlled remotely and are ideal for automated systems requiring frequent adjustments. While highly accurate, they depend on electrical power and involve complex installation. Motor valves are commonly used in HVAC systems, industrial automation, and process control where reliable flow regulation is necessary.
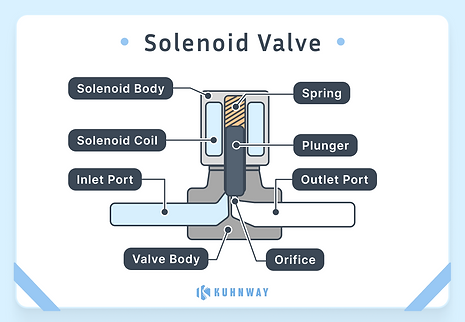
Solenoid valves are actuated valves controlled electrically by energizing a solenoid coil to create magnetic attraction, which then moves a plunger to open or close the valve. They offer rapid response times and are well-suited for automated systems.
However, they are typically used for smaller flow rates and may be sensitive to fluid impurities. Common solenoid valve applications include irrigation systems, pneumatic controls, and industrial processes where quick, reliable fluid control is needed. They can also be found in everyday appliances, like ice makers, and dishwashers.
-
Hydraulic-actuated Valve
Hydraulic-actuated valves are actuated valves that use pressurized hydraulic fluid, normally oil, to move the valve mechanism. This type of actuation functions similarly to pneumatic systems, using fluid pressure to generate thrust that drives the piston. They provide smooth, powerful operation and are suitable for controlling large valves in high-pressure and high-flow systems.
However, they require a hydraulic power source and regular maintenance. These valves are commonly used in heavy machinery, oil and gas industries, and marine applications, where robust and reliable operation is critical.
-
Pneumatically-actuated Valve
Pneumatically actuated valves rely on compressed air or gas as an external pressure source to drive a piston within a closed cylinder or diaphragm, enabling the valve to fully open or close. They offer quick, reliable control and are safe for hazardous environments since they don’t require electricity. They rely on a consistent air supply and need maintenance to prevent leaks. These valves are widely used in manufacturing, chemical processing, and automation systems for fast and frequent operations.
Comparison Chart for Different Types of Valves and Uses
Name
Opening Methods
Pros
Cons
Uses
Gate Valve
Linear
Reliable, minimal pressure loss, durable
Not suitable for throttling, slow operation
Water supply, oil pipelines, industrial plants
Globe Valve
Linear
Precise flow control, excellent sealing
Higher pressure drop, expensive, bulky
Steam systems, cooling lines, fuel processes
Needle Valve
Linear
Highly precise, robust for low-flow systems
Not for high-flow systems, prone to clogging
Instrumentation, chemical dosing, lab experiments
Pinch Valve
Linear
Cost-effective, leak-resistant, ideal for abrasive fluids
Limited to tube material properties, not for high pressure
Mining, wastewater treatment, food processing
Diaphragm Valve
Linear
Handles corrosive fluids, clean, easy to maintain
Not suitable for high-pressure systems, diaphragm wear
Water treatment, pharmaceuticals, food industries
Ball Valve
Rotary
Fast operation, tight sealing, compact
Not ideal for throttling, harder to clean
Hydraulic systems, gas pipelines, high-pressure applications
Butterfly Valve
Rotary
Lightweight, cost-effective, quick operation
Limited throttling at high pressure differences
Large pipelines, HVAC systems, fire protection
Plug Valve
Rotary
Simple design, durable, handles various fluids
Large sizes need significant force, regular maintenance
Chemical processing, natural gas, oil refineries
Check Valve
Automatic
Prevents backflow, protects equipment, simple operation
Risk of water hammer, debris can affect sealing
Pump discharge lines, water systems, fuel pipelines
Pressure-Reducing Valve
Automatic
Stable pressure control, no external power needed
Pressure drops, requires maintenance
Water distribution, industrial setups, irrigation
Pressure-Relief Valve
Automatic
Prevents overpressure, ensures safety
Limited fine control, needs regular inspection
Boilers, pressure vessels, piping systems
Pressure-Sustaining Valve
Automatic
Maintains critical upstream pressure
Incorrect settings can affect downstream pressure
Water systems, industrial processes
Motor Valve
Actuated
Precise and reliable, suitable for automation
Dependent on electricity, complex installation
HVAC systems, industrial automation, process control
Solenoid Valve
Actuated
Fast response, versatile, ideal for automation
Sensitive to impurities, limited flow rates
Irrigation, pneumatic controls, industrial processes
Hydraulic-Actuated Valve
Actuated
Powerful, smooth operation for high-pressure systems
Requires hydraulic power source, regular maintenance
Heavy machinery, oil and gas, marine applications
Pneumatically Actuated Valve
Actuated
Quick control, safe for hazardous environments
Requires consistent air supply, potential for leaks
Manufacturing, chemical processing, automation systems
Other Common Valves Classification
In addition to motion and actuation methods, valves are commonly classified based on pressure and temperature ratings, end connection types, and body materials.
-
Pressure and Temperature Ratings
Valves are engineered to operate safely and efficiently within specific pressure and temperature ranges.
Pressure ratings, as standardized by ASME B16.34, define the maximum allowable working pressure (MAWP) for various materials at specific temperatures. These ratings are categorized into classes like 150, 300, 600, 900, and beyond, ensuring compatibility with system requirements. Temperature ratings depend heavily on valve materials as this is also regulated by the ASME standard.
For example, a Class 150 valve made from ASTM A216 WCB carbon steel can handle pressures up to 285 psi at 100°F, with allowable pressure decreasing as temperature increases. Conversely, a Class 1500 valve of the same material can withstand pressures up to 3,750 psi at 100°F. This classification system ensures that valves are selected appropriately for their intended pressure and temperature conditions, maintaining safety and efficiency in piping systems.
Here are some common valves:
-
Low-Pressure Valves: These valves are typically designed for systems operating at pressures up to 1.6 MPa (approximately 232 psi). They are commonly used in applications such as residential plumbing, water treatment, and irrigation systems, where the pressure requirements are relatively modest.
-
High-Pressure Valves: High-pressure valves are engineered to withstand significantly higher pressures, often exceeding 10 MPa (about 1,450 psi). They are essential in industries like oil and gas and chemical processing, where systems operate under environments with extreme pressure.
-
Cryogenic Valves: Designed for extremely low temperatures (below -238°F), cryogenic valves are used in applications involving liquefied gases, such as liquid nitrogen, ensuring proper sealing and operation at sub-zero temperatures.
-
High-Temperature Valves: These valves can operate in environments with temperatures exceeding 1000°F, making them suitable for steam services and power generation facilities.
-
End Connection
The way a valve connects to a piping system impacts its installation, maintenance, and suitability for specific applications. Here’s an overview of common end connection types:
-
Flanged End Valves: Flanged valves have protruding flanges that bolt directly to the pipe flanges, forming a strong, leak-proof connection. They are easy to install, remove, and maintain, making them ideal for high-pressure or large-diameter pipelines. These valves are commonly found in water distribution and industrial systems.
-
Threaded End Valves: Threaded valves feature internal or external screw-threaded ends that connect directly to threaded pipes. They are perfect for smaller pipe sizes, low-pressure systems, and temporary installations. Their simplicity makes them common in residential plumbing and irrigation setups.
-
Welded End Valves: These valves are welded permanently into the piping system, creating a seamless, leak-free joint. Welded valves are best suited for high-pressure, high-temperature applications where reliability and durability are critical, such as in oil and gas pipelines.
-
Clamped Valves: Clamped valves use clamps to secure the valve to the piping system. This design allows for quick assembly and disassembly, making them a preferred choice in sanitary industries like food processing and pharmaceuticals, where regular cleaning is essential.
-
Wafer Valves: Wafer-style valves fit between pipe flanges and are secured with bolts passing through the flanges. They are compact, lightweight, and cost-effective, making them suitable for applications with space constraints, such as HVAC systems and water pipelines.
-
Body Material
The material composition of valve bodies is crucial, as it directly impacts their durability, compatibility with various fluids, and performance under different operating conditions. Choosing the wrong material can lead to corrosion, leaks, or even system failure. Here are some common materials used in valve construction:
Metallic Valves
-
Carbon Steel: Valves made from carbon steel are widely used due to their strength and ability to withstand high pressures and temperatures. They are suitable for standard services and are commonly used in industrial applications.
-
Stainless Steel: Types like 304 and 316 stainless steel offer excellent corrosion resistance, making them ideal for applications involving corrosive media. 316 stainless steel, in particular, contains molybdenum, enhancing its resistance to pitting in chloride-containing solutions.
-
Cast Iron and Ductile Iron: These materials are typically used for low to medium-pressure applications. Cast iron is suitable for temperatures between -15°C to +200°C, while ductile iron can handle temperatures from -30°C to +350°C.
-
Brass: Known for their good corrosion resistance and excellent machinability, making them suitable for various applications. However, they are susceptible to de-zincification in specific environments. It is also a popular choice for low-pressure systems due to its durability and ease of manufacturing.
-
Copper: Offers excellent thermal conductivity, corrosion resistance, and ductility, making it ideal for high-temperature fittings joined by soldering or brazing in chemical and water systems.
-
Bronze: Stronger than copper, bronze resists pitting corrosion, and is easily cast and machined, making it a standard for pressure-rated valves in industrial and chemical applications.
Non-Metallic Valves
-
PVC (Polyvinyl Chloride): PVC valves are lightweight, cost-effective, and exhibit excellent corrosion resistance, making them suitable for chemical processing and water treatment applications. They are generally used in low-pressure and low-temperature settings.
-
PTFE (Polytetrafluoroethylene): Known for its high chemical resistance and non-reactivity, PTFE is used in applications involving highly corrosive fluids. It also has a wide temperature tolerance, enhancing its versatility.
Alloy Valves
-
Inconel: This nickel-chromium-based alloy offers exceptional resistance to oxidation and corrosion at high temperatures, making it suitable for extreme environments like power generation and chemical processing.
-
Hastelloy: Known for its outstanding resistance to a wide range of chemical processes, Hastelloy valves are indispensable in industries dealing with highly corrosive substances, such as pharmaceuticals and petrochemicals.
How to Select the Right Type of Valve: What Else to Consider
We’ve covered valve classifications based on opening methods, pressure ratings, temperature ranges, materials, and connection types, all of which are critical to finding the right fit for your system. But beyond these basics, there are other important considerations. Let’s dive into these factors to help you make the best choice for your needs.
First, determine the valve's role in regulating flow, whether it is used for on/off control, throttling, or preventing backflow. For precise control over flow rates or positions, control valves equipped with positioners or modulating actuators offer fine-tuned control over process variables, ideal for applications with stringent performance requirements. For quick on/off operation, ball or butterfly valves are excellent choices. If preventing backflow is the priority, use a check valve.
The sizing for valves is also important. Considering both the physical dimensions and internal flow rates to ensure a proper fit and accurate flow control. A valve that’s too small can restrict flow and cause upstream back-pressure, while an oversized valve reduces flow control precision. It is best to match the connector diameter and flow rate to your system needs.
The media being controlled—whether liquid, gas, slurry, or corrosive chemicals—affects valve selection as well. For example, pinch valves are ideal for slurries, while solenoid valves are excellent for automated control of gases and liquids in irrigation or industrial systems. Naturally, this affects the materials for valves, for example, when monitoring harsh or corrosive materials, materials like PTFE and PFA are suitable due to their ability to withstand such conditions.
Finally, balancing cost and quality is just as crucial. While it may be tempting to focus on lower initial costs, investing in high-quality valves can significantly reduce long-term expenses, such as replacements. Also, consider the maintenance requirements—valves with simpler, reliable designs are easier to service, be cleaned regularly, and help reduce downtime and operational costs. Thoughtful selection not only enhances efficiency but also extends the valve's lifespan, offering better value over time.
Kuhnway: Elevate Your Operations with Superior Valves
Valves are essential components that keep countless systems running smoothly, from industrial plants to everyday plumbing. We've explored the various kinds of valves in piping, classifications, and their unique applications, showing how each one plays a critical role in controlling and optimizing fluid flow.
Understanding their features and selecting the right type ensures system efficiency, safety, and reliability. With this knowledge, you can make confident project choices and achieve the best possible results. Of course, you will always need an experienced valve supplier for high-quality products, reliable performance, and expert guidance to ensure your systems operate efficiently and effectively.
At KUHNWAY Corporation, we understand that selecting the right valve is crucial for achieving efficiency, safety, and reliability in your systems. Whether it's a 2-way solenoid valve for precise automation or an electric actuator for seamless operation, we've highlighted the wide range of valve types and their unique roles to guide you in making informed choices.
We take pride in our decades of expertise and innovation, ensuring that every product we deliver meets the highest standards of quality and performance. As you've learned about the diverse classifications and applications of valves, we’re here to provide the solutions that best fit your needs.
Let KUHNWAY be your trusted valve manufacturer in powering your projects with the most advanced and reliable valves on the market. Contact us today, and let’s work together to achieve excellence in every system you build. Your success is our commitment!
Full Guide to All Types of Valves: Functions and Applications
Learn the various types of valves, and their classifications by motion, function, actuation, features, and uses, ensuring optimal selection for your needs.